DE
- Industries
- Finance
Nearshore software development for finance—secure, scalable, and compliant solutions for banking, payments, and APIs.
- Retail
Retail software development services—e-commerce, POS, logistics, and AI-driven personalization from nearshore engineering teams.
- Manufacturing
Nearshore manufacturing software development—ERP systems, IoT platforms, and automation tools to optimize industrial operations.
- Finance
- What we do
- Services
- Technologies
- Collaboration models
Explore collaboration models customized to your specific needs: Complete nearshoring teams, Local heroes from partners with the nearshoring team, or Mixed tech teams with partners.
- Way of work
Through close collaboration with your business, we create customized solutions aligned with your specific requirements, resulting in sustainable outcomes.
- About Us
- Who we are
We are a full-service nearshoring provider for digital software products, uniquely positioned as a high-quality partner with native-speaking local experts, perfectly aligned with your business needs.
- Meet our team
ProductDock’s experienced team proficient in modern technologies and tools, boasts 15 years of successful projects, collaborating with prominent companies.
- Our locations
We are ProductDock, a full-service nearshoring provider for digital software products, headquartered in Berlin, with engineering hubs in Lisbon, Novi Sad, Banja Luka, and Doboj.
- Why nearshoring
Elevate your business efficiently with our premium full-service software development services that blend nearshore and local expertise to support you throughout your digital product journey.
- Who we are
- Our work
- Career
- Life at ProductDock
We’re all about fostering teamwork, creativity, and empowerment within our team of over 120 incredibly talented experts in modern technologies.
- Open positions
Do you enjoy working on exciting projects and feel rewarded when those efforts are successful? If so, we’d like you to join our team.
- Candidate info guide
How we choose our crew members? We think of you as a member of our crew. We are happy to share our process with you!
- Life at ProductDock
- Newsroom
- News
Stay engaged with our most recent updates and releases, ensuring you are always up-to-date with the latest developments in the dynamic world of ProductDock.
- Events
Expand your expertise through networking with like-minded individuals and engaging in knowledge-sharing sessions at our upcoming events.
- News
- Blog
- Get in touch
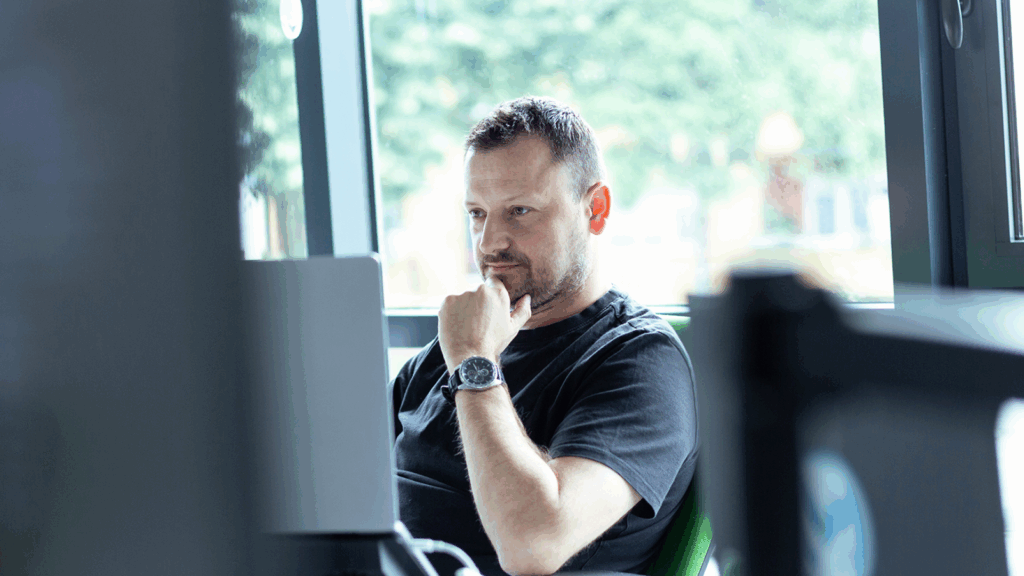
19. May 2025 •6 minutes read
The digital shift in Sweden’s manufacturing sector: Trends and forecasts for 2025
ProductDock
For Sweden’s manufacturing sector, driving innovation has never been more important. Industry 4.0 is accelerating the shift towards smart manufacturing, where digital advancements such as IoT, artificial intelligence and big data are streamlining operations and creating more efficient production systems. As automation, data analytics, and interconnected systems continue to rise, industries like automotive, electronics, and machinery are increasingly leveraging modern technology to ensure higher production capacity, reduce downtime, and optimize resource utilization. A study shows that by the end of 2025, Sweden’s manufacturing sector could achieve SEK 160-220 billion annually through the wider adoption of these technologies, signaling growth across the broader manufacturing industry.
From ERP systems to IoT platforms and automotive software, manufacturing companies are accelerating transformation to build resilience and drive growth. In particular, advanced technologies like machine learning and real-time analytics are becoming essential assets.
In this blog, we dive deep into the transformative trends shaping Sweden’s manufacturing landscape and offer insights into how digitalization will drive the industry’s evolution in the years to come.
The rise of robotic process automation and AI-driven solutions
Automation is a cornerstone of digital transformation in manufacturing, and its adoption is rapidly growing, with 70-80% of manufacturing industries already automating their processes. Robotic process automation (RPA) plays a key role in this shift. It enables manufacturers to automate repetitive tasks, reduce human errors and enhance overall operational efficiency. RPA frees up employees from mundane tasks, allowing them to focus on more strategic and creative tasks. For example, RPA bots can automate processes such as data entry, supply chain logistics and inventory management.
Advanced robotic systems and automation technologies are enabling factories to operate around the clock with fewer workers, significantly reducing operational costs while increasing efficiency. In Sweden, this trend is clearly evident in the growing automotive industry robotic market, which is projected to reach US$159.76m by 2025. Revenue in this sector is expected to show an annual growth rate of 15.69%, bringing the market size to US$286.17 million by 2029.
The integration of AI and machine learning further accelerates the evolution of robotic systems. According to the study by the National Association of Manufacturers, 72% of surveyed manufacturers reported increased operational efficiency and reduced costs after deploying AI.
Combined with AI-driven solutions, robotics can take on more complex tasks that were traditionally performed manually. For example, AI technologies can carry out product quality inspections, optimize production schedules, predict maintenance needs, and improve quality control. By analyzing massive datasets, these systems can uncover patterns and make data-driven predictions, driving further optimization of manufacturing processes.
Studies show that 78% of manufacturers have implemented or are planning to invest in supply chain software that enables advanced supply chain planning, better collaboration with suppliers and enhanced visibility. This software has been ranked among the top 5 technologies for driving the most significant ROI.
A real-world example of this transformation comes from Maria Strömsdörfer, a product owner at an automotive company in Germany. She explained that their company collected large amounts of data from various areas, and to better utilize it, they needed a custom software solution. Partnering with a nearshore software development company, they developed a custom solution that included front-end and back-end development using open-source technologies. This software allowed the company to operate more efficiently and make more informed decisions.
The emergence of smart factories and autonomous production systems
In traditional manufacturing, it is often difficult to keep track of everything happening on the shop floor. With numerous processes, employees and production lines running simultaneously, misalignment and inefficiencies are common. With the rise of digital technologies, connected devices, and advanced automation systems, smart factories that optimize material flows, facilitate production management and allow performance monitoring in real-time. By using different technologies, such as IoT devices, ERP systems, and AI technologies, factories achieve automated workflows and become self-regulating systems, reducing the need for human involvement in repetitive tasks. This shift allows better communication, faster decision making and less downtime.
In Sweden, the manufacturing sector has increasingly recognized the benefits of adopting smart factories. Many companies are leveraging these advanced technologies to modernize their processes, making production not only more efficient but also more sustainable. Beyond improving efficiency, smart factories contribute to reducing emissions, which aligns with Sweden’s environmental goals and promotes a greener future.
One example of a company embracing this shift is the KAMAX Group, a leading producer of high-strength fasteners for the automotive industry. KAMAX has digitized its plant to increase efficiency and transparency. They have developed a digital dashboard that provides employees with real-time access to production data and ensures smoother operations and better decision-making. Additionally, they built a KPI board to track performance, identify potential issues and drive continuous improvement throughout the plant.
The integration of IoT in manufacturing operations
The integration of IoT in the manufacturing industry has become a transformative trend, particularly in industries like machinery, automotive and electronics. When IoT is connected with machinery, robots and other factory units, they enable seamless communication between devices, allowing them to autonomously coordinate operations, share data and make informed decisions. IoT platforms give operators real-time visibility and control over manufacturing processes, improving efficiency, safety and reducing risks of unscheduled maintenance.
According to McKinsey’s research, IoT applications in manufacturing could generate an economic impact ranging from $1.2 to $3.7 trillion annually by the end of 2025.
Deloitte’s findings highlight that predictive maintenance enabled by IoT leads to a 70% reduction in equipment breakdowns and a 25% decrease in maintenance costs. This explains why 78% of supply chain leaders are increasingly seeking technological solutions to accelerate production and delivery timelines and automate repetitive tasks.
Sweden’s manufacturing companies follow this trend. They increasingly collaborate with an experienced software development team that specializes in identifying and implementing the most effective digital solutions to optimize their workflows.
As Đorđe Mijailović, a full-stack developer working on business analytics tools for a global leader in the automotive industry, puts it:
“The great thing about working on a manufacturing project is that I had the freedom to make key decisions about how to solve customer challenges. It wasn’t just about technical decisions and coding, but about being deeply involved in identifying problems alongside the business team and then solving them through code”.
Challenges and opportunities in the Swedish market
As companies expand their global reach, managing the intricacies of sourcing, logistics, and inventory is becoming increasingly challenging. This has created opportunities for solutions such as real-time data tools and predictive analytics. According to a 2024 report on industrial product manufacturers, big data, advanced analytics, supply chain digitalization, and data management will play an important role in shaping the industry in the years ahead.
In Sweden, the ongoing digitalization of operations is driving a growing demand for tailored software solutions, particularly for modern ERP systems and supply chain optimization. Sweden’s commitment to innovation further underscores the fact that the government is backing AI advancements through initiatives like AI Sweden. Major companies, such as Volvo, have already begun embedding AI into their operations, using it to automate processes, improve predictive maintenance and improve customer service.
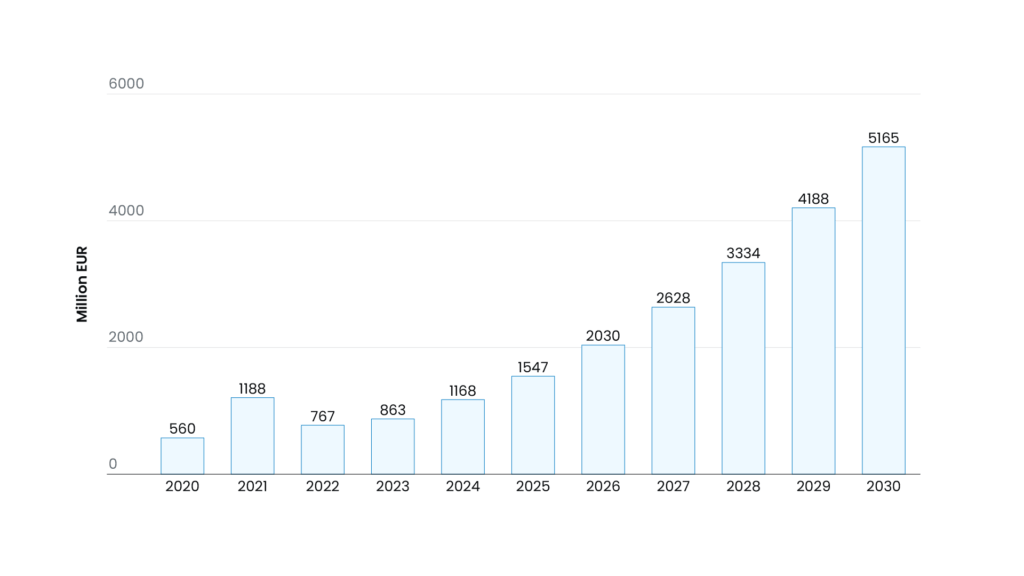
Source: Market study: The Swedish market for IT services, Open Trade Gate Sweden, October 2024
As a country committed to achieving net-zero emissions by 2045 and consistently ranking high on the SDG (Sustainable Development Goals) Index, Sweden is well-positioned to adopt technologies such as IoT-enabled energy management systems, smart grids, and sustainable supply chain solutions. These innovations not only enhance efficiency but also cater to the market’s growing demand for green solutions, attracting eco-conscious customers.
Despite the numerous opportunities, some obstacles remain. Many companies still rely on outdated infrastructure, creating significant challenges in integrating new technologies. The process of transitioning from legacy systems to more modern solutions can be both complex and costly, requiring careful planning and investment. Additionally, as digital technologies continue to advance, the demand for skilled talent in Sweden remains a significant challenge. Manufacturers will need to prioritize finding and retaining top tech talent to stay competitive.
Conclusion
The rise of digital transformation opens numerous opportunities for manufacturing companies in Sweden. By adopting automation software, IoT platforms, ERP systems, machine learning for AI predictive maintenance and other advanced tools, manufacturing companies can unlock new levels of efficiency, precision and scalability. These innovations drive more efficient production processes, increase resource utilization, ultimately generating significant value.
However, it is crucial for manufacturers to remain mindful of the challenges ahead. Strategic investment in digital infrastructure, upskilling the workforce and partnering with reliable software providers will be essential to maximizing the potential of digitalization.
Balancing technology and sustainability efforts will be key for establishing leadership in the Swedish manufacturing industry and ensuring long-term growth in this rapidly dynamic market.